Background
Formula Student is a prestigious international competition where university student teams design and develop racing cars resembling Formula-style vehicles. These cars compete in various performance disciplines, highlighting innovation, technical expertise, and teamwork. As part of the DHBW Engineering project, we have developed an all-electric, all-wheel-drive racing car that fully complies with Formula Student regulations. This project emphasizes the integration of advanced technologies to achieve superior driving dynamics and exceptional on-track performance.
One of the significant challenges in developing an electric all-wheel-drive vehicle is the precise, real-time control of drive force, which must be distributed individually to each wheel. To address this challenge, we developed a state estimation module that continuously monitors and estimates key vehicle parameters, including speed, acceleration, position, and the forces acting on each wheel.
This data feeds into the torque vectoring system, which dynamically distributes torque to each of the four wheels, optimizing traction and stability. By constantly assessing the vehicle’s condition, the system ensures that each wheel receives the optimal amount of torque, guaranteeing maximum grip under all conditions
A schematic representation of the key sensors involved in the condition estimation process is shown in Figure 2.1.
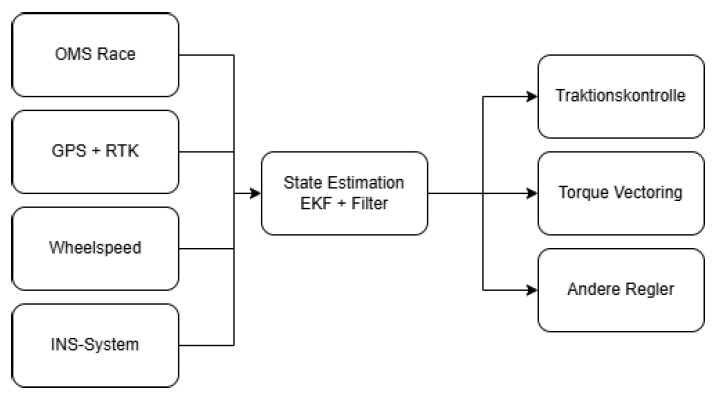
Figure 2.1: Sensor topology
Use of Measurement Data
A central element of our estimation methodology is speed estimation, which plays a crucial role in operating a high-performance all-wheel-drive system, particularly for controlling cornering and acceleration. In addition to the vehicle’s overall speed, it is essential to measure or estimate the individual speeds of each wheel to maintain optimal wheel slip and ensure driving stability under demanding conditions.
Speed estimation is achieved through sensor fusion technology, combining data from various sources such as:
- An Inertial Measurement Unit (IMU)
- A GPS receiver
- Wheel speed sensors
- A highly precise ground speed sensor
At the core of our condition estimation process lies the Extended Kalman Filter (EKF), which enables reliable and robust sensor fusion. The IMU serves as the primary data source, while GPS, wheel speed sensors, and an additional IMU system function as secondary sources to validate and secure measurements.
To enhance our EKF architecture, we integrated the OMS Race ground speed sensor, which provides a high measurement frequency of 1000 Hz and features improved noise suppression. This makes it an ideal addition to our system, enabling us to achieve unparalleled accuracy and stability in speed estimation, even under challenging conditions.
The higher measurement frequency of the OMS Race Sensor, compared to the older Kistler Correvit sensor (which operates at 250 Hz), allows for significantly more precise and dynamic detection of vehicle behavior. The integration of the OMS sensor with the IMU further enhances its capabilities, particularly in measuring the vehicle’s speed and angle of inclination. This combination enables a higher dynamic range, resulting in improved estimation of the vehicle’s dynamics.
One of the standout advantages of the OMS Race Sensor is its seamless integration into our EKF-based condition estimation framework. This ensures exact synchronization with the system’s internal processing rate, eliminating the need for interpolation and thereby enhancing overall data fidelity.
In the previous season (2023/2024), our speed estimates relied primarily on the Kistler Correvit sensor. However, discrepancies of up to 5 km/h were observed between the data from the Kistler Correvit sensor and the OMS Race Sensor. Additionally, the noise characteristics of the Kistler Correvit sensor were noticeably inferior. These limitations prompted us to adopt the OMS Race Sensor as the primary sensor for state estimation in the current season. This shift has improved measurement accuracy and significantly reduced errors in both speed and handling estimation.
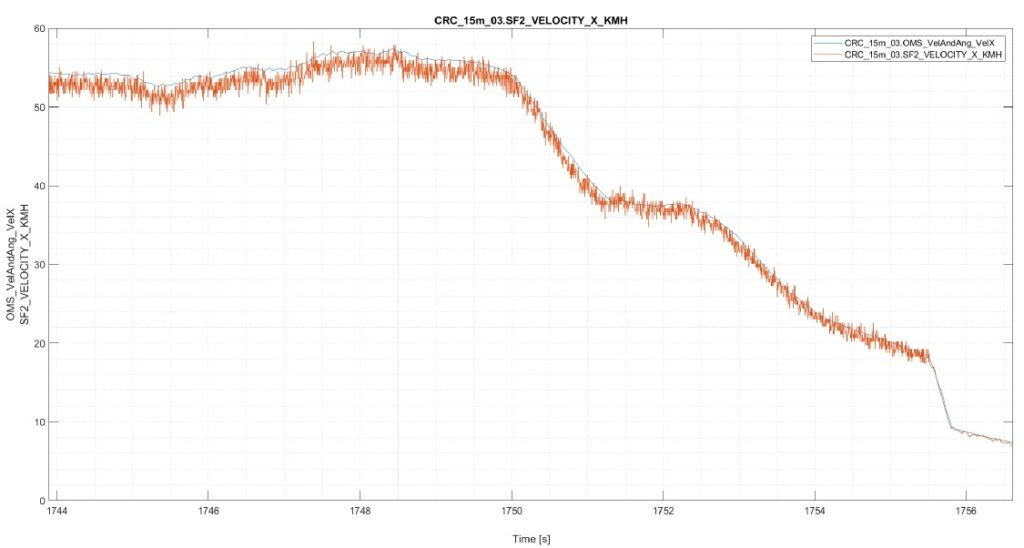
Figure 2.2: Comparison of OMS Race with Kistler Correvit SF2
Installing the Sensor in the Vehicle
Given the high optimization of our vehicle for weight and aerodynamics, selecting a suitable mounting location for the OMS Race Sensor posed a significant challenge. It was crucial to position the sensor in a location that would provide reliable measurements while minimizing any potential aerodynamic disturbances.
After careful consideration, we opted to install the sensor near the rear axle, as illustrated in Figure 2. This location ensures accurate data collection without compromising the vehicle’s aerodynamic profile. Furthermore, the OMS Race Sensor shares the same construction as the Kistler Correvit SF2, enabling a straightforward, plug-and-play installation process.
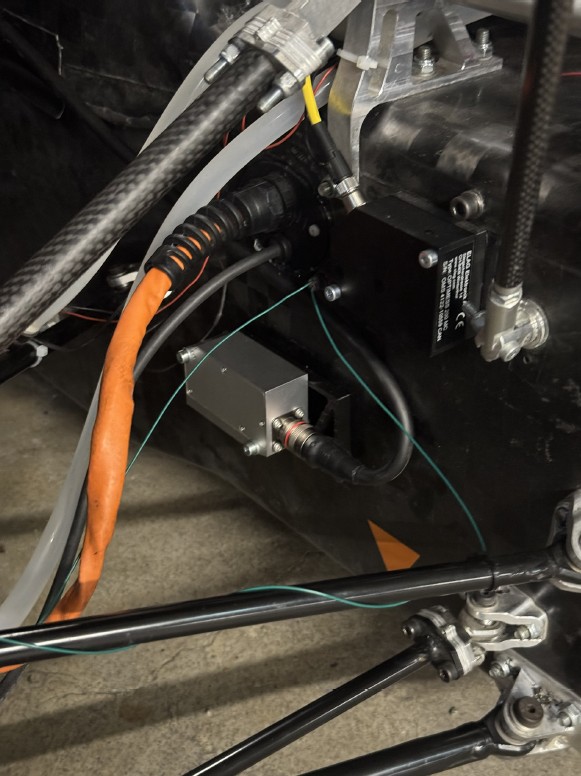
Figure 3.1: Installation position on the vehicle
By precisely defining the sensor’s position relative to the vehicle’s center of gravity (COG) in our CAD environment, we ensured that all positional deviations are accounted for in the data processing. This approach allows measured values for speed and acceleration to be automatically corrected for the sensor’s offset from the vehicle’s COG, thereby eliminating the need for manual post-processing.
Additionally, the system offers the option to save multiple sensor presets. This feature facilitates rapid adaptation to changes in the sensor’s installation position and enables seamless transfer of the system to other vehicles.
Summary
The integration of the OMS Race Sensor and the optimization of our condition estimation methods have significantly enhanced the accuracy of our vehicle dynamics measurements. These improvements have made a substantial contribution to the vehicle’s performance by enabling faster and more precise adaptation of torque to changing driving conditions, thereby improving both driving stability and safety.
We highly recommend the OMS Race Sensor to all Formula Student teams seeking to validate and enhance their traction control systems.
Author: Benni Stauder, Technical Project Manager, DHBW Engineering Stuttgart